Chemicals are a part of our everyday lives, and we use them for various purposes. However, many chemicals can be hazardous to our health and the environment if not handled correctly. The CLP Regulation is a set of rules designed to ensure that chemicals are labelled correctly and that people who use them know of potential hazards. In this ultimate guide for CLP Labels, we will explore the CLP Regulation, why it is important, what it covers, and how to create compliant and effective CLP labels.
What is the CLP Regulation?
The CLP Regulation, short for the Classification, Labelling and Packaging Regulation (EC) 1272/2008, is a set of regulations established by the European Union (EU) to ensure the safe handling, transport, and use of chemicals. The regulation applies to all substances, from household cleaning products to industrial chemicals, and requires that they be classified and labelled according to their potential hazards.
Before the introduction of the CLP Regulation, chemicals were classified according to the Dangerous Substances Directive (DSD) and the Dangerous Preparations Directive (DPD), which were both phased out in June 2015. The CLP Regulation replaced these directives and brought the EU in line with the United Nations’ Globally Harmonized System of Classification and Labelling of Chemicals (GHS).
There are three main elements to the CLP Regulation: classification, labelling, and packaging. Classification involves identifying the hazards of a chemical based on its physical, chemical, and toxicological properties. The classification system used by the CLP Regulation includes hazard classes such as explosive, flammable, toxic, and corrosive.
Labelling involves communicating the identified hazards to anyone who may come into contact with the chemical. This is done through the use of standardised pictograms, hazard statements, and precautionary statements on the packaging and labelling of chemical products.
Packaging involves ensuring that the chemical is safe to transport and store. This includes requirements for the strength and durability of packaging and restrictions on the size of containers for certain types of hazardous chemicals.
It is important to note that the CLP Regulation is not just a set of guidelines or recommendations; it is a legal requirement for anyone who manufactures, imports, or supplies chemicals in the EU. Failure to comply with the regulation can result in legal action, including fines and even imprisonment.
Why is the CLP Regulation important?
The CLP Regulation is important because it ensures that chemicals are used and handled safely in the EU, protecting the health of humans and the environment. The CLP Regulation requires manufacturers and importers to classify and label their chemical products, providing essential information about the hazards of a substance or mixture, as well as the appropriate precautions that need to be taken to ensure safe handling and use.
By providing clear and consistent information about the hazards associated with chemicals, the CLP Regulation helps prevent accidents and incidents that could harm people or the environment. It also facilitates the free movement of goods within the EU by harmonising the classification and labelling of chemicals, making it easier for companies to sell their products across borders.
Furthermore, the CLP Regulation plays a critical role in implementing other EU legislation related to chemicals, such as REACH (Registration, Evaluation, Authorisation, and Restriction of Chemicals) and the Biocidal Products Regulation (BPR). Together, these regulations form a comprehensive framework for ensuring the safe use of chemicals in the EU.
What are CLP Labels?
CLP Labels are used to communicate information about the hazards associated with chemical substances and mixtures in the European Union (EU). The CLP regulation requires manufacturers and importers of chemical products to provide clear and consistent information about the hazards of their products on the label. This includes:
- Product identifiers: As a general rule, the term used for identifying the substance or mixture should be the same as that used in the safety data sheet.
- Signal words: A signal word indicates the relative level of severity of a particular hazard. The label must include the relevant signal word in accordance with the classification of the hazardous substance or mixture: more severe hazards require the signal word ‘Danger’ while less severe hazards require the signal word ‘Warning’.
- Nominal quantity: Unless this quantity is specified elsewhere on the package, it should be part of the label (i.e. the weight)
Hazard statements, the appropriate precautionary statements, and a section for supplemental information will be used where applicable.
- Hazard statements: The Hazard Statements provide the consumer with a direct warning as to what the mixture may do – the nature of the hazard. If a Hazard Statement is triggered by a particular ingredient at a specific concentration, it MUST be included on the label, along with its relevant pictogram.
- Precautionary statements: The Precautionary Statements are a set of instructions that advise the customer how to avoid or minimise the hazards that the hazardous mixture may cause.
- Statements: The regulations state that ‘relevant’ precautionary statements should be included, some being mandatory, some recommended, and others advised. For Example, Allergen Information should also be included on the label if applicable.
- Hazard pictograms: A hazard pictogram is a pictorial presentation to communicate information on the hazard concerned.
- Supplier details: The Supplier Details include the supplier’s name, address, and telephone number.

What are CLP hazard pictograms and how to display them?
A CLP hazard pictogram is a visual representation of information that combines a warning symbol with specified colours to tell us about the potential harm a given item or mixture may do to our health or the environment. A total of 9 hazard pictograms are used in the CLP Regulation, each representing a different type of hazard.
Each pictogram is represented by a symbol on a white background with a red diamond border. The symbol itself is black and shows an image that represents the specific hazard. For example, the flammable pictogram shows a flame, while the corrosive pictogram shows an image of corrosion.
To display the CLP hazard pictograms on a label, manufacturers and importers must ensure that the pictogram is clearly visible and meets the size and formatting requirements specified in the CLP Regulation. The pictogram must also be accompanied by a signal word, such as “danger” or “warning”, and a hazard statement that provides additional information about the specific hazard associated with the chemical product.
If you must include a lot of pictograms on your CLP label, you can limit the number of them by paying attention to the principles of precedence. For example, an exclamation mark shouldn’t be displayed if your label includes a skull and crossbones. The website of the European Chemicals Agency has more details on this.
Let’s consider some of the common CLP Pictograms:
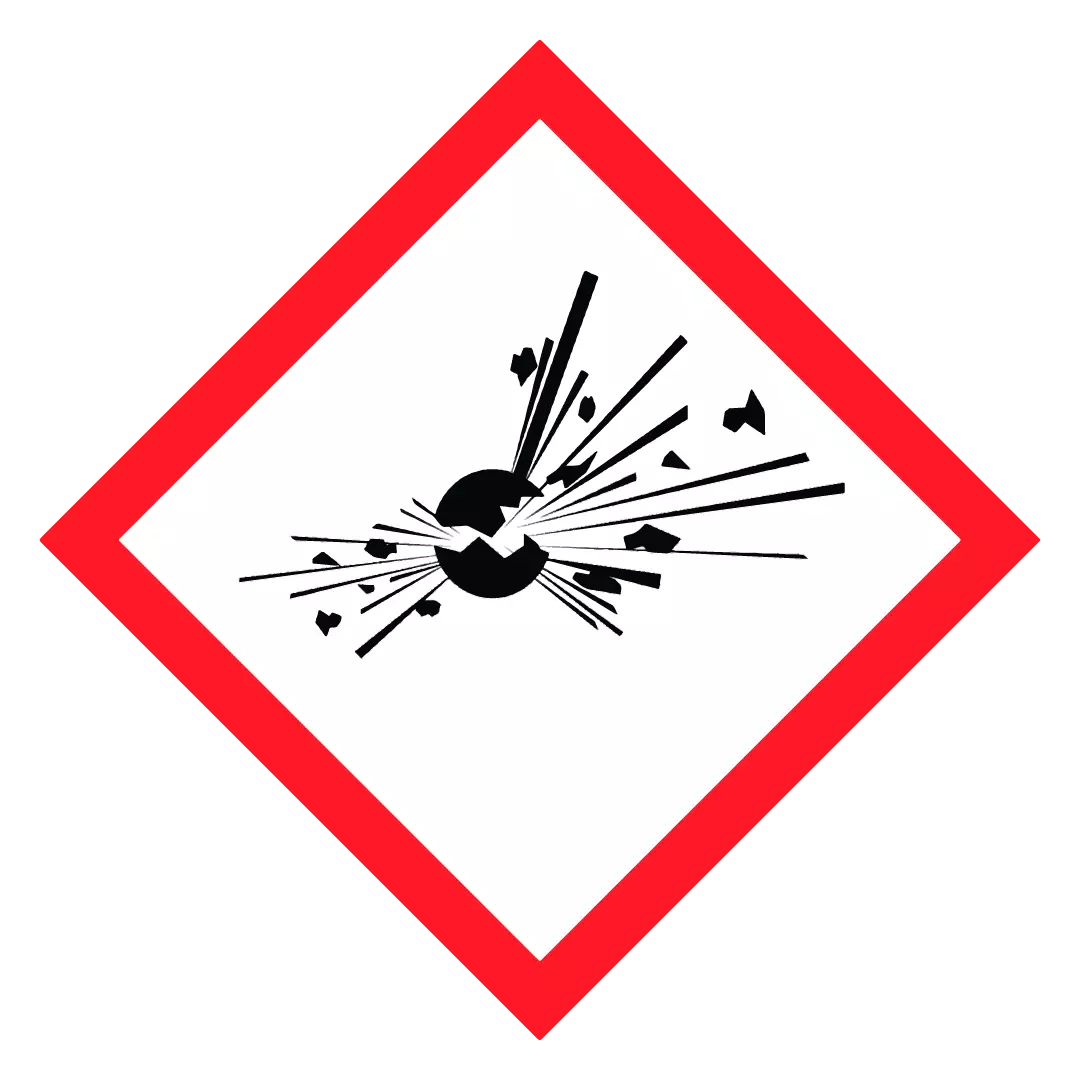
Explosive
These substances can react even without the participation of atmospheric oxygen with heat development and fast generation of gases. They explode easily or deflagrate fast.

Flammable
Products with this pictogram are extremely flammable. Be particularly careful with the product in the presence of heat, fire, or near open flames. Incorrect storage can lead to self-ignition.
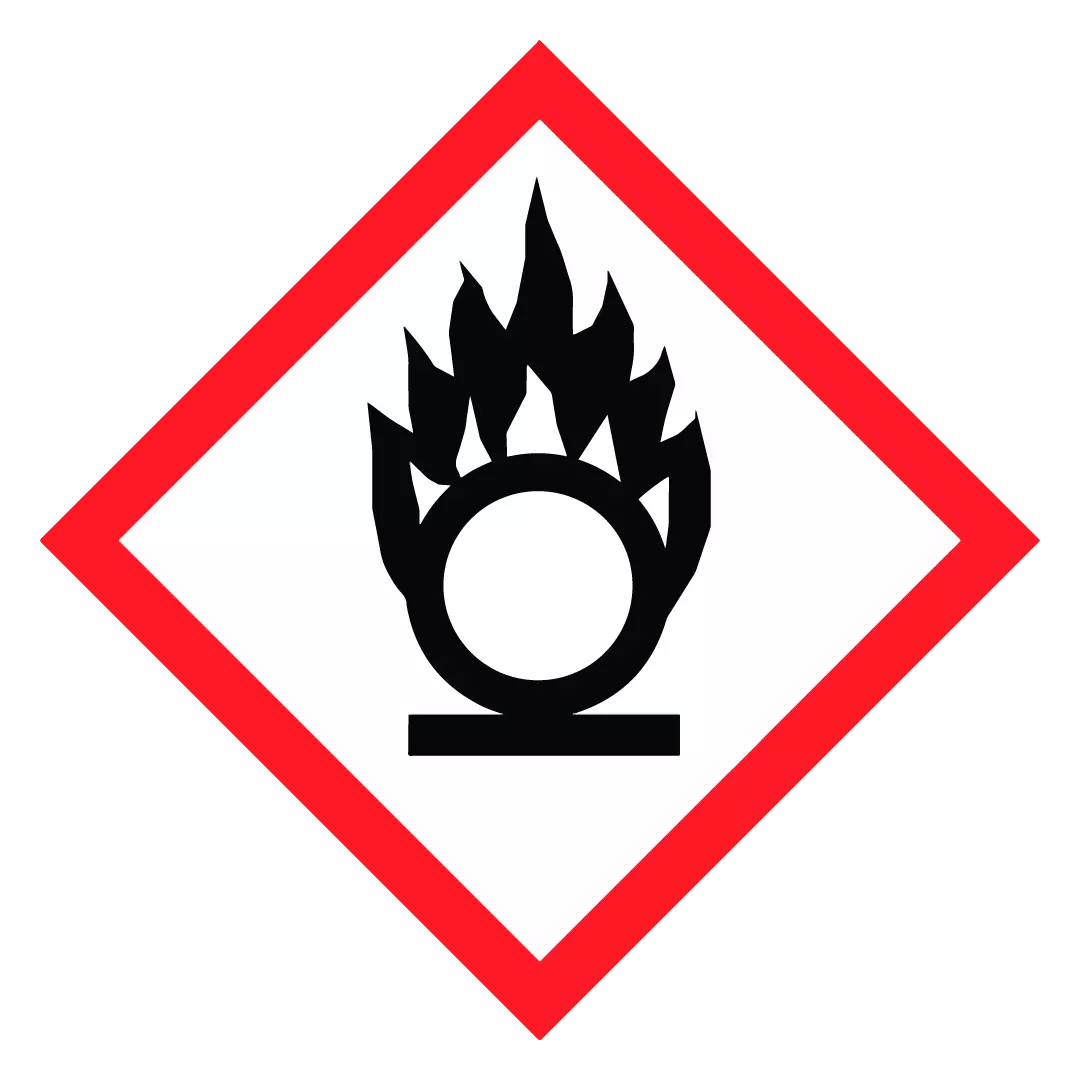
Oxidising
If these chemicals come into contact with other materials, particularly flammable materials, they react with strong heat development. They can cause or intensify fires or explosions. Incorrect storage can lead to explosions.

Gas under pressure
The picture of a gas cylinder indicates gases under pressure. If stored incorrectly or exposed to intense heat, they can explode. These also may be refrigerated, liquefied gases which can cause cryogenic burns or injuries.
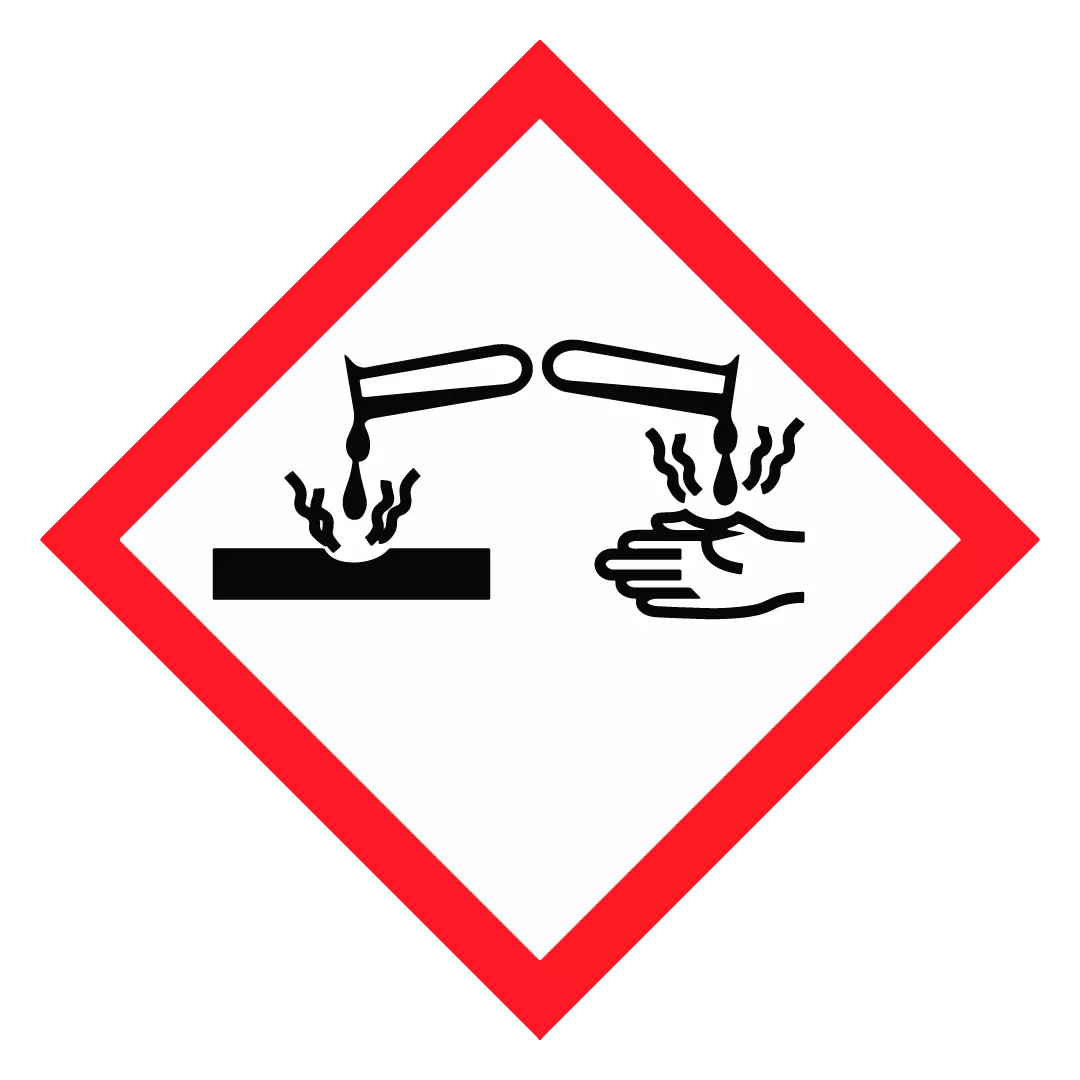
Corrosive
Risk of severe skin burns or serious eye damage. The pictogram also indicates that these chemicals are corrosive to metals.
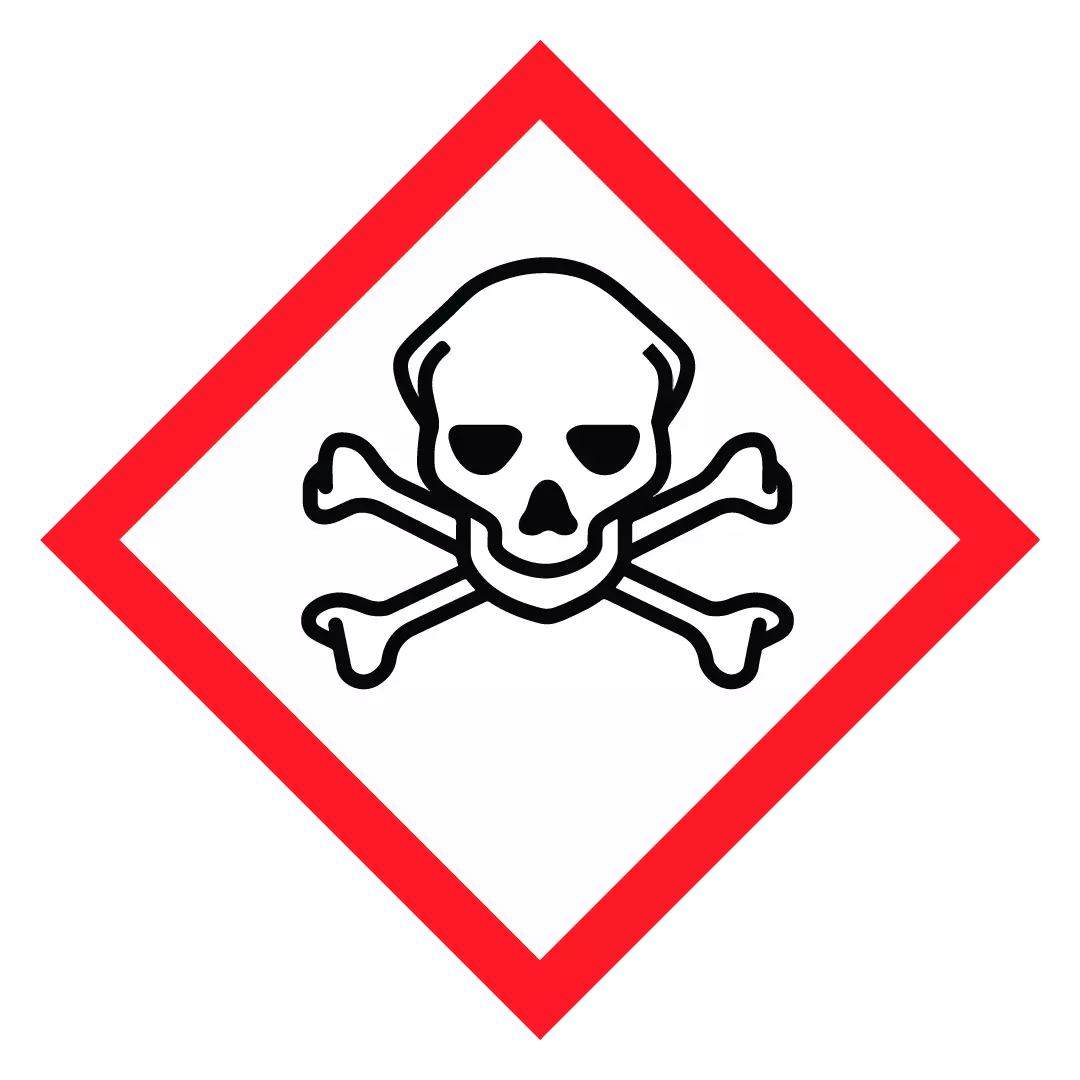
Acute toxicity
Even in the smallest quantities, certain chemicals can lead to life-threatening poisoning if they come in contact with skin and are swallowed or inhaled.

Health hazard
The exclamation mark warns you about various health hazards. The substances can be harmful if swallowed, in contact with the skin, or inhaled. These substances may cause skin or eye irritation or trigger an allergic reaction. Also, they can be hazardous to the ozone layer.
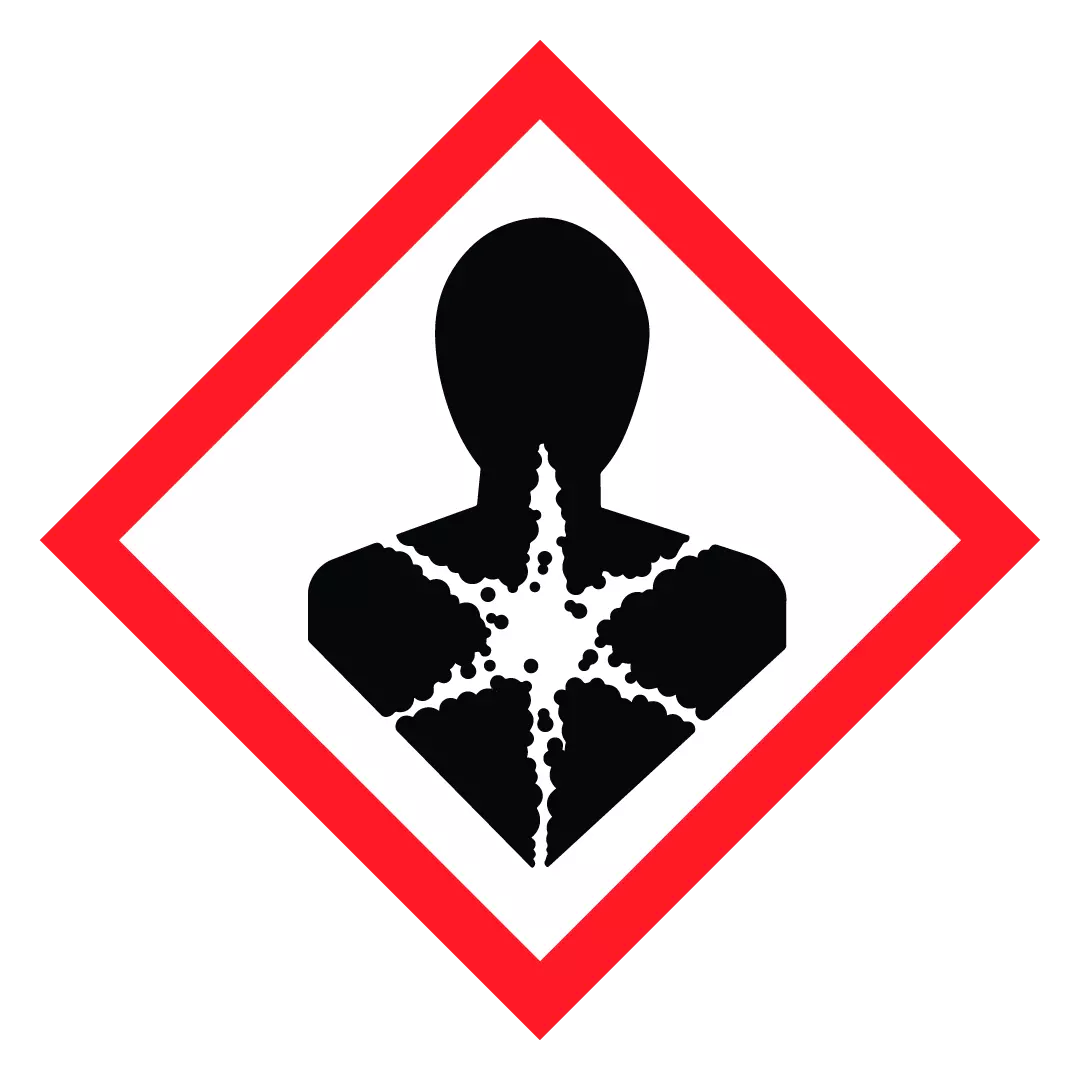
Serious health hazard
This pictogram indicates the risk of severe damage to health. The product poses serious health hazards; for example, it may cause cancer or damage the unborn child. Products with this pictogram must be handled with particular care.

Hazardous to the environment
Very toxic to aquatic life, possibly with long-lasting effects. Always dispose of products with this pictogram appropriately and never discard them with normal household waste or empty them into wastewater drains.
Creating compliant CLP Labels
Creating compliant CLP labels involves several steps, including determining the hazards associated with the chemical, selecting the appropriate hazard pictograms and signal words, and ensuring that the label meets the requirements of the CLP Regulation. The label must also include information on the product identifier, the supplier’s name and address, and any precautionary statements or instructions for use.
Tips for creating effective CLP Labels
- Understand the classification of the chemical: Before creating a CLP label, it’s essential to understand the classification of the chemical. Understanding the classification will help you determine the appropriate hazard statements, pictograms, and precautionary measures to include on the label. You can find this information on the Safety Data Sheet (SDS) or consult with a chemical safety expert.
- Use clear and concise language: When creating a CLP label, use clear and concise language that is easy to understand. Avoid technical jargon and use simple language that conveys the potential hazards associated with the chemical.
- Include pictograms: Pictograms are graphical symbols used to indicate specific hazards associated with the chemical. They are mandatory on CLP labels and must be displayed prominently. Ensure that the pictograms are clear and easy to understand.
- Include hazard and precautionary statements: Hazard statements describe the type of risks that a particular chemical carries. Precautionary statements provide advice on how to handle the chemical safely. Both statements are mandatory on CLP labels and must be written clearly and concisely.
- Ensure legibility: CLP labels must be legible, meaning the font size must be appropriate for the label size. The label must also be printed in a language that the user understands.
What is a Safety Data Sheet (SDS) and how does it relate to CLP?
A Safety Data Sheet (SDS) is a document that provides detailed information about a chemical’s properties, hazards, and handling precautions. The SDS is used by manufacturers, importers, and suppliers to communicate the potential hazards associated with the chemical. The SDS must accompany the chemical when it is shipped and must be available to downstream users who handle the chemical.
Where should CLP Labels be placed?
If the chemical substance or mixture is packaged in a small container, such as a bottle or can, the label may be attached directly to the container rather than the outer packaging. In this case, the label should still be clearly visible and legible, and should not obscure any important information on the container, such as the product name or batch number.
In addition to being placed on the outer packaging or container, CLP labels may also be required to be displayed in other locations, such as in the workplace where the product is used or on transport documents if the product is being transported. This ensures that those who handle or transport the product are aware of the hazards associated with the product and can take appropriate precautions to prevent accidents or incidents.
Do you need a CLP Label, SDS, or both?
CLP labels are used to identify a chemical’s hazards and communicate this information to anyone who may come into contact with it. These labels are required by law in many countries and must include specific information, such as the name of the chemical, hazard pictograms, signal words, and precautionary statements. The purpose of CLP labels is to provide a quick and easy way for anyone handling a chemical to identify its potential hazards and to take appropriate precautions.
An SDS is typically required by law for all hazardous chemicals and is intended to provide comprehensive information for anyone who may need to handle or come into contact with the chemical. On the other hand, an SDS provides more detailed information about a chemical’s properties, including its physical and chemical properties, and information on its potential health and environmental hazards. An SDS also provides instructions on handling, storing and transporting the chemical safely, as well as first aid measures in case of exposure.
So, whether you need a CLP label, SDS, or both, the answer depends on the situation. If you are handling or storing hazardous chemicals in the workplace, you will likely need both CLP labels and an SDS to comply with regulations and to ensure the safety of yourself and others. CLP labels provide quick and easy identification of hazards, while an SDS provides more comprehensive information on handling and storage.
In summary, it’s important to prioritise safety when working with hazardous chemicals. CLP labels and an SDS are two important tools that can help ensure that everyone who comes into contact with a chemical knows its potential hazards and how to handle it safely. By using both CLP labels and an SDS, you can help to prevent accidents and protect yourself and others from the dangers of hazardous chemicals.
Conclusion
Understanding CLP labels is essential to safely handling and using chemical substances and mixtures in the European Union. The CLP Regulation governs the classification, labelling, and packaging of chemical products to protect the health of people and the environment. CLP labels provide clear and consistent information about the hazards associated with chemical products, using standardised symbols and signal words to communicate potential risks to those who handle or use the products.
As a manufacturer or importer of chemical products in the EU, you must ensure that your products are classified, labelled, and packaged in compliance with the CLP Regulation. This includes understanding the hazard categories, using the correct pictograms and signal words, and ensuring the label is clear and legible. By following these guidelines, you can help ensure that your products are safe for use and meet the necessary regulatory requirements.
As a consumer or user of chemical products, it is important to read and understand the information provided on CLP labels and to take the necessary precautions when handling or using these products. By working together, manufacturers, importers, and users of chemical products can help to ensure that these products are used safely, protecting the health of people and the environment.