What is a Safety Data Sheet (SDS)?
What does an SDS contain?
Here’s a breakdown of the 16 sections present in an SDS:
- Identification: This section includes the product’s name, intended use, supplier’s contact information, and emergency phone numbers. It ensures easy identification and communication in case of incidents.
- Hazard identification: Here, potential hazards associated with the substance are detailed. This includes information about physical, health, and environmental hazards, as well as the classification according to regulations like the Globally Harmonized System (GHS).
- Composition/ingredients: This section lists the ingredients of the substance or mixture, along with their specific concentration ranges. It’s critical for understanding potential exposure risks and compatibility with other substances.
- First aid measures: In case of exposure, this section outlines immediate first aid procedures. It includes information on inhalation, ingestion, skin contact, and eye exposure, providing essential guidance for responders.
- Fire-fighting measures: Details regarding appropriate firefighting techniques, extinguishing agents, and precautions to take in case of a chemical fire are provided here.
- Accidental release measures: This section advises on containment, cleanup, and disposal procedures for spills or leaks. It helps minimise environmental impact and ensure safe handling during such incidents.
- Handling and storage: Guidelines for safe handling, storage conditions, and precautions to prevent potential hazards are outlined in this part. Proper storage and handling minimise risks to personnel and the environment.
- Exposure controls/personal protection: This section includes recommended exposure limits, ventilation requirements, and personal protective equipment (PPE) within the workplace necessary to mitigate potential exposure risks.
- Physical and chemical properties: Details about the substance’s appearance, odour, melting/boiling points, and solubility are provided. This information aids in understanding the substance’s behaviour and compatibility.
- Stability and reactivity: Potential reactivity hazards, stability concerns, and incompatible materials are outlined here, helping prevent dangerous reactions.
- Toxicological information: This section presents data on the substance’s potential health effects, including acute and chronic toxicity, irritation, and sensitization.
- Ecological information: Information on the substance’s potential impact on the environment, such as aquatic toxicity and persistence. This assists in ensuring proper environmental management.
- Disposal considerations: Guidance on proper disposal methods and regulatory considerations for waste management is provided in this section.
- Transport information: Information related to transporting the substance, including packaging requirements, hazardous material classifications, and any restrictions, is outlined.
- Regulatory information: This section covers relevant regulatory information, such as hazard classifications, labelling requirements, and other compliance-related data.
- Other information: Additional information, such as revision history, references, and any important notes, is included here.
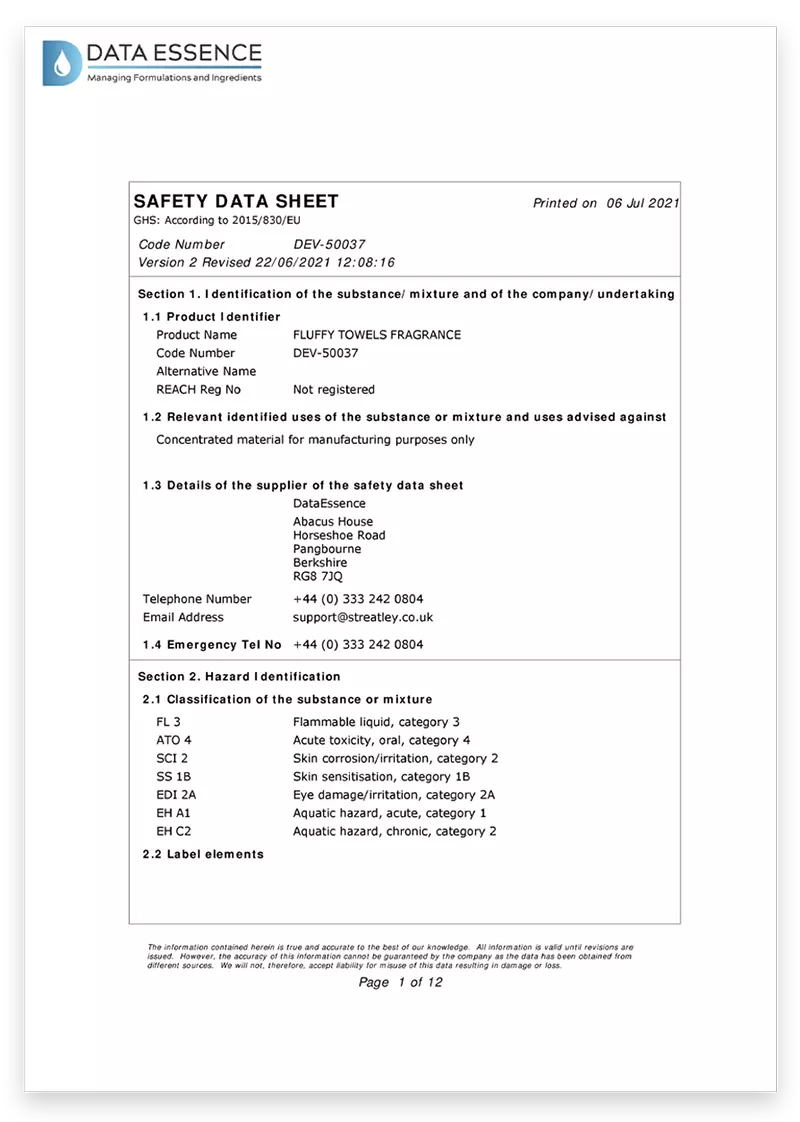
How to read an SDS?
This information helps ensure you are examining the correct SDS for a particular substance. Next, focus on hazard identification. This section outlines the potential dangers associated with the substance, including physical and health hazards. Understanding these risks is vital for implementing appropriate safety measures. Additionally, review information regarding safe handling and storage practices. Here, you will find instructions on how to safely use and store the substance to minimise exposure risks.
Lastly, familiarise yourself with emergency procedures in case of accidents or spills involving the substance. If you work in a larger organisation, communicating this information to staff who handle the substance is a priority for their personal health and safety.
How to update an SDS?
When updating a Safety Data Sheet (SDS), there are several crucial considerations to ensure accuracy and compliance. Firstly, it is essential to stay informed about regulatory changes regarding hazard communication and chemical classification. This involves monitoring updates from regulatory agencies such as ECHA, HSE and OSHA. Another critical consideration is maintaining accurate information on chemical ingredients. Regularly review and update the composition of your products to reflect any changes in ingredients or their concentrations.
Furthermore, it is important to conduct thorough research on the potential hazards associated with your products. This includes reviewing toxicological data, conducting studies if necessary, and ensuring that hazard statements and precautionary measures are up-to-date. Regularly assessing the format and layout of your SDS is also crucial. Ensure that it complies with current standards while providing clear instructions for safe handling, storage, disposal, and emergency response.
Best practices for maintaining updated SDS
Ensuring that Safety Data Sheets (SDS) are regularly updated is crucial for maintaining a safe working environment and complying with regulatory requirements. Here are some best practices to follow:
- Establish a process: Designate a responsible person or team to oversee SDS management and updates. Develop a clear process that includes reviewing, revising, and reissuing SDS as needed.
- Stay informed: Regularly monitor regulatory changes related to hazard communication and chemical safety. Subscribe to relevant industry newsletters, attend training sessions, or join professional networks to stay up-to-date.
- Collaborate with suppliers: Maintain open lines of communication with your suppliers regarding any changes in chemical compositions or hazards associated with their products. Ensure that your supplier understands your intended use of the substance so that they may adapt the SDS to your specific use and setting. Request updated SDS promptly and ensure they meet your requirements.
- Train employees: Educate employees on the importance of SDS updates and how to access the most recent versions. Using information within the SDS, ensure that employees understand the protocols of safely working with substances.
Learn how to produce SDS for your products!
How to translate an SDS?
When translating an SDS into another language, meticulous attention to detail and accuracy is imperative to ensure that the safety information is effectively conveyed across linguistic barriers. Here’s a comprehensive guide on how to proficiently translate a Safety Data Sheet:
- Expertise in technical terminology: Engage professional translators who possess a solid grasp of both the source and target languages, along with expertise in technical terminology related to chemicals and safety. This ensures that the translated content maintains accuracy and clarity.
- Maintain original intent: Preserve the original intent and meaning of the content while translating. It’s vital to ensure that safety information, hazard descriptions, and precautionary measures remain consistent with the original language.
- Cultural relevance: Consider the cultural nuances of the target audience. Some symbols, idiomatic expressions, and units of measurement might require adaptation to suit the cultural context without compromising accuracy.
- Regulatory compliance: Ensure that the translated SDS complies with the regulations of the target country or region. Safety regulations, labelling requirements, and hazard classifications can vary, so the translated version must reflect these changes accurately.
- Formatting consistency: Maintain the original formatting and layout in the translated version. This includes headings, section numbering, tables, and bullet points. Consistency in presentation aids readability and navigation.
- Proofreading and validation: Enlist experts who are fluent in the target language and have a background in chemical safety to review and validate the translated SDS. This step helps identify and rectify any inaccuracies or misinterpretations.
- Contextual accuracy: Ensure that all chemical names, descriptions, and instructions are accurately translated. Misinterpretation of even a single term can lead to confusion and potential safety hazards.
- Maintain clarity: Focus on clarity and simplicity in translation. Complex sentence structures or technical jargon should be translated into terms that are easily understandable for the target audience.
- Pictograms and icons: When translating pictograms, hazard symbols, and safety icons, ensure that they maintain their universal meaning and comply with local regulations. Some symbols might have cultural associations that need to be considered.
- Adhere to language laws: If the target language has specific laws regarding language usage for safety information, ensure that these laws are followed while translating the SDS.
- Quality control: Conduct thorough reviews of the translated content to catch any inconsistencies, errors, or discrepancies. A final review by a linguistic expert can provide additional assurance of translation accuracy.
- Multilingual SDS: If the SDS is being translated into multiple languages, maintain consistency across all versions. This consistency fosters better understanding and reduces the risk of misinterpretation.
- Document the process: Keep a record of the translation process, including any changes made and the reasoning behind them. This documentation is valuable for quality control and future reference.
- User testing: Before finalising the translated SDS, consider conducting user testing with individuals who are proficient in the target language. Their feedback can help identify any potential confusion or areas that need improvement.
- Continuous improvement: Regularly review and update the translated SDS to reflect any changes in regulations, language usage, or best practices. A proactive approach ensures ongoing accuracy.
When is an SDS required?
The requirement for a Safety Data Sheet arises in various scenarios, primarily dictated by regulatory standards and guidelines. While regulations might differ slightly across industries and regions, some common situations necessitating the presence of an SDS include:
- Chemicals and hazardous materials: When dealing with chemicals or hazardous materials in the workplace, having an SDS is non-negotiable. Whether it’s a corrosive cleaning agent, a flammable solvent, or a potentially toxic substance, the SDS acts as a beacon of information. From outlining the composition of the substance to detailing its physical and chemical properties, the SDS equips individuals with the necessary knowledge to handle the material safely.
- Employee safety and training: Prioritising employee safety is paramount for any responsible employer. When employees are required to work with or be in proximity to hazardous substances, it is mandatory to provide them with the relevant information to ensure their well-being. An SDS not only imparts knowledge about potential hazards but also guides employees on the correct usage, storage, and disposal procedures.
- Regulatory compliance: Regulations and standards set forth by authorities such as ECHA (European Chemicals Agency), HSE (Health and Safety Executive) and OSHA (Occupational Safety and Health Administration) mandate the use of SDSs for certain hazardous materials. Failing to comply with these regulations, such as the EU REACH Regulation, can lead to severe penalties, tarnishing a company’s reputation and potentially causing harm to employees.
- Emergency preparedness: Emergencies can strike when least expected. In situations involving spills, leaks, fires, or other incidents involving hazardous materials, an SDS becomes an invaluable resource. First responders and emergency personnel can quickly access essential information from the SDS to make informed decisions, thereby minimising the risks and mitigating potential harm.
- Transportation of hazardous materials: When hazardous materials are transported, whether within the company premises or externally, having an SDS on hand is crucial. It ensures that all parties involved, including drivers, handlers, and recipients, are aware of the potential hazards and the necessary precautions to take.
Who is responsible for the SDS?
Manufacturers and distributors
Regulatory agencies and compliance experts
Chemical experts and professionals
Employers and workplace safety managers
Employers and workplace safety managers are responsible for implementing the information provided in the SDS within their respective organisations. They ensure that employees have access to SDS for the chemicals they work with and that proper training is provided for safe handling and storage. These professionals bridge the gap between the technical language of the SDS and practical application within the workplace.
Employees
Employees are crucial in putting SDS information into action. By thoroughly reading and understanding the SDS, they can make informed decisions about handling chemicals safely, responding to emergencies, and minimising risks. Following the guidelines outlined in the SDS contributes to a safer work environment and protects individuals from potential harm.
Dealing with the Safety Data Sheets (SDS) from suppliers doesn’t have to be a headache. Download our tips for managing the SDS to ensure safety and compliance!
How to store the SDS?
Consider using digital platforms or cloud-based systems that offer advanced search functionalities and real-time updates. Furthermore, the storage solution should comply with local regulations regarding SDS retention periods and accessibility requirements. By carefully considering these factors, you can ensure a secure and efficient method for storing your SDS documentation.
Legislation and regulations of SDS
To ensure uniformity and harmonization across the European Union (EU), two key regulations have been established: the Registration, Evaluation, Authorisation, and Restriction of Chemicals (REACH) regulation and the Classification, Labelling, and Packaging (CLP) regulation.
The REACH Regulation
The REACH (Registration, Evaluation, Authorisation, and Restriction of Chemicals) Regulation is a comprehensive legislation enacted by the European Union (EU) to ensure the safe use of chemicals. Its primary objective is to protect human health and the environment from potential risks associated with chemical substances. REACH requires manufacturers and importers to register their substances with the European Chemicals Agency (ECHA). This registration process involves providing detailed information about the properties, uses, and potential hazards of each substance.
The key principles of the EU REACH Regulation were retained in UK REACH Regulation. It is important to note that EU REACH and UK REACH operate independently of each other. UK REACH regulates chemicals placed on the market in GB. EU REACH continues to apply in NI.
The collected data enables authorities to evaluate and manage risks effectively. Furthermore, REACH promotes the substitution of hazardous chemicals with safer alternatives whenever possible. It also encourages companies to communicate information about chemical safety along their supply chains through Safety Data Sheets (SDS). By enhancing transparency and accountability throughout the supply chain, REACH empowers businesses and consumers to make informed decisions regarding chemical substances.
The CLP Regulation
The Classification, Labelling, and Packaging (CLP) Regulation is a vital piece of legislation within the context of chemical safety in the European Union (EU). It was introduced to align with the Globally Harmonized System of Classification and Labelling of Chemicals (GHS), aiming to ensure a consistent approach to hazard classification, labelling, and packaging of substances and mixtures. The CLP Regulation sets out specific criteria for classifying hazardous chemicals based on their physical, health, and environmental effects.
The EU CLP Regulation as amended, is retained in GB law. Goods placed on the market in the EU, EEA and NI are subject to EU CLP Regulation. The GB CLP Regulation applies to GB based manufacturers, importers, downstream users and distributors supplying the GB market, including those from NI who directly supply the GB market.
It also provides guidelines for accurately labelling these chemicals with standardised pictograms, signal words, hazard statements, and precautionary statements. By adopting this harmonized system across the EU member states, it enhances communication regarding chemical hazards throughout the supply chain. Furthermore, the CLP Regulation mandates that manufacturers or importers notify relevant authorities about substances they place on the market if they meet certain criteria.
Conclusion
Safety Data Sheets (SDS) are more than just documents; they’re essential tools for safeguarding lives and the environment. Whether you’re an employee, or responsible for managing hazardous materials, understanding the SDS is critical. This guide has equipped you with a comprehensive understanding of the SDS, its components, and its significance. By adhering to the information provided in the SDS, you contribute to a safer, healthier world.
Learn how to produce SDS for your products!